En un mot, le processus Jidoka peut être décrit comme un processus d’ « automatisation » avec un cerveau humain. L’article ci-dessous explique le processus Jidoka à l’aide d’exemples.
Le premier Jidoka
Le métier à tisser automatique, inventé par Sakichi Toyoda, le fondateur de Toyota, en l’an 1902, peut être considéré comme le premier exemple de Jidoka. Dans cette innovation, si les fils venaient à manquer ou à se rompre, le processus du métier à tisser était arrêté automatiquement et immédiatement.
Au début de la production de masse par chaîne de montage, les cycles de travail étaient surveillés par un opérateur humain. Avec l’augmentation de la concurrence, Toyota a apporté un changement important à ce processus en automatisant les cycles des machines afin que les opérateurs humains soient libres d’effectuer d’autres tâches. Le système de production Toyota dispose de nombreux outils permettant d’obtenir des produits et des services efficaces.
Développés au fil des années, ces outils visent à réduire l’effort humain et à automatiser les machines pour augmenter la productivité. Le Jidoka est l’un de ces outils sans lequel une fabrication efficace serait pratiquement impossible, à ce jour. L’article ci-dessous explique tout sur le processus Jidoka.
Le concept d’autonomie
- Pour commencer, comprenez que l’autonomie et l’automatisation sont différentes l’une de l’autre.
- Selon la définition de l’autonomation, il s’agit d’un processus « auto-fonctionnant » ou « auto-contrôlé ». C’est une caractéristique qui contribue au processus de Jidoka.
- L’automatisation est le processus où le travail est encore surveillé par un opérateur, où les erreurs peuvent encore être apparentes, et où la détection et la correction prennent plus de temps.
- L’automatisation résout deux points principaux. Premièrement, elle réduit l’interférence humaine, et deuxièmement, elle empêche les processus de faire des erreurs. Ces points ont été énumérés ci-dessous.
Défaut de produit
- Ordinairement, lorsqu’un défaut se produit, un travailleur le détecte et rapporte plus tard le problème.
- L’automatisation permet à la machine d’arrêter le cycle lorsqu’une pièce défectueuse est rencontrée.
Dysfonctionnement du processus
- Si toutes les pièces ou composants traités ne sont pas ramassés à la fin du cycle, la machine pourrait être confrontée à des problèmes, et le processus pourrait s’arrêter, et il faudrait un certain temps avant que le travailleur ne se rende compte que le processus a été interrompu à cause d’une erreur mineure.
- En cas d’autonomisation, si la pièce précédente n’a pas été ramassée lors de l’éjection, la machine donne un signal ou arrête complètement le cycle.
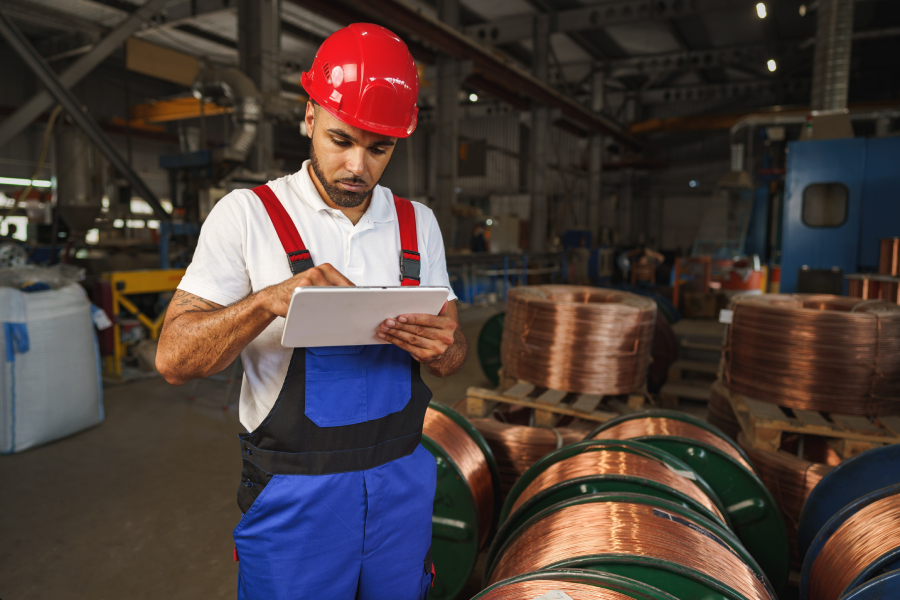
Une introduction au Jidoka
L’évolution vers le Jidoka
- Jidoka peut être défini simplement comme une « automatisation humanisée ». L’autonomisation n’est qu’un autre terme pour Jidoka.
- Il est utilisé dans différents contextes. Il est principalement utilisé pour détecter les défauts et arrêter immédiatement la production ou le processus de fabrication. Elle corrige le défaut et trouve des solutions pour que le défaut ou l’erreur ne se reproduise plus.
- Le concept, comme mentionné précédemment, a été inventé par Sakichi Toyoda. Son but est de réduire l’erreur humaine et le jugement par la détection et la correction automatique des erreurs.
- Il a été mis au point pour réduire le nombre d’erreurs humaines.
- Il a été développé pour éradiquer la perte de temps due à l’observation humaine du processus, du transport, de l’inventaire, de la correction du défaut, etc.
- Aujourd’hui, avec le Jidoka, les lignes de production sont devenues nettement plus efficaces, et le gaspillage de marchandises et de stocks a également été réduit.
Autres outils et termes Toyota
- Vous devez garder à l’esprit est que Andon, Poka-yoke, Just-in-time, etc, sont tous des outils inventés par Toyota. Jidoka est également l’un de ces outils, et il englobe certains des autres également, comme Andon et Poka-yoke.
- Jidoka a été développé pour minimiser les erreurs qui ont pu être causées par des observations humaines.
- Rappellez-vous qu’Andon n’est pas un exemple de jidoka, mais un outil important. Il affiche l’état actuel du travail – si le processus est fluide, ou s’il présente un quelconque dysfonctionnement, ou s’il y a des problèmes de produit, etc.
- La relation entre Andon et Jidoka a été expliquée plus loin dans l’article.
- Similaire à Jidoka, le juste-à-temps est un autre outil important et constitue l’un des piliers cruciaux du TPS.
- Il adhère à quel produit est requis, quand il est requis, et quelle quantité est requise.
- Le » takt time » est un principe important – il fait référence au temps qui devrait être pris pour fabriquer un produit sur une machine.
- Line Stop Jidoka est un terme qui s’applique au processus dans les usines de fabrication automobile.
- Il est appelé ainsi car il interrompt et arrête toute la ligne (processus) lorsqu’un défaut est découvert.
Les éléments du Jidoka
Genchi Genbutsu
- C’est l’un des éléments importants du Jidoka.
- Le principe de base du Genchi Genbutsu est de voir réellement le problème. Cela implique d’aller à la source profonde du problème.
- C’est une étape importante du processus de Jidoka : découvrir pourquoi le défaut s’est produit en premier lieu.
Andon
- Comme indiqué dans la section précédente, Andon est une représentation visuelle du processus actuel.
- Il indique si le processus s’exécute selon les normes ou s’il y a une faille potentielle.
- Selon l’état, il émet des signaux électroniques. Si le signal est négatif, les travailleurs comprendront qu’il y a un problème dans le processus.
- La machine s’arrête, immédiatement bien sûr, et les travailleurs peuvent arrêter la production jusqu’à ce que le défaut du processus soit corrigé.
Normalisation
- Le principal objectif du Jidoka est d’augmenter la qualité de la production. C’est ce dont traite la normalisation.
- Il s’agit de développer des stratégies qui adhèrent à la perfection et à la qualité.
- Lorsqu’un défaut est découvert, il n’est pas seulement réparé, mais des efforts sont également entrepris pour qu’il ne se reproduise pas, et la qualité et la norme du même produit sont maximisées.
Poka-yoke
Ce concept est également appelé mistake-proofing ou error-proofing ; les dispositifs poka-yoke sont conçus pour éviter les erreurs qui pourraient se produire pendant la production.
Les principes
Le processus Jidoka
Comme on le voit sur la figure ci-dessus, sans Jidoka, la pièce défectueuse continue à être produite et éjectée. Ce n’est qu’après l’éjection que le travailleur peut se rendre compte que le produit est défectueux et qu’il arrête alors le processus.
Dans cette figure, avec Jidoka, la lumière Andon s’allume fortement, indiquant que le produit est défectueux. Le processus est immédiatement arrêté et les mesures nécessaires sont prises.
Détecter
- Il s’agit de détecter le problème.
- La machine est fixée avec les bons composants afin que l’anomalie soit immédiatement identifiée.
- Pour cette étape, les machines peuvent être fixées avec des capteurs, des cordons électriques, des boutons poussoirs, des dispositifs électroniques, ou peuvent être alimentées avec des instructions appropriées pour identifier si un produit est défectueux.
Arrêter
- Une fois qu’un défaut a été repéré, la machine s’arrête immédiatement.
- La machine est conçue pour s’arrêter d’elle-même, aucun personnel ou ouvrier n’a besoin de l’arrêter physiquement.
- Le fait qu’un défaut a été détecté est indiqué par des signaux. Une fois que c’est fait, le personnel pourrait se précipiter sur le site pour savoir pourquoi le processus a été arrêté.
Réparation
- Lorsque la machine s’arrête, la ligne de production doit être arrêtée.
- Vous pouvez vous demander pourquoi toute la ligne doit être arrêtée à cause d’une ou plusieurs pièces défectueuses. Cela est fait parce qu’il y a une probabilité que des pièces ou des composants défectueux aient été fabriqués en même temps que la pièce ou le composant défectueux.
- Pour éviter cette surproduction et ce gaspillage de matériel et d’équipement, la ligne de production est arrêtée.
- Après cela, des démarches sont entreprises pour régler le problème. Parfois, il peut s’agir d’un petit pépin, alors que parfois, il peut y avoir un problème majeur.
- Une fois l’erreur réparée, la production reprend.
Investigation
- La dernière étape du Jidoka, plutôt vitale, consiste à enquêter sur la source du problème.
- Vous devez trouver des réponses aux questions suivantes : « Pourquoi le défaut s’est-il produit ? », « De quel type de défaut s’agit-il ? », « Comment le réparer ? », « Que peut-on faire pour l’empêcher ? », etc. Les outils d’analyse des causes profondes sont largement utilisés pour aller au fond du problème.
- À travers ce processus, des efforts sont entrepris pour trouver la meilleure solution pour le défaut, et pour empêcher qu’il ne se produise en premier lieu.
- À mesure que les enquêtes et les recherches se multiplient, de meilleures méthodes de fabrication sont découvertes, de meilleures techniques de résolution des problèmes sont inventées, et la qualité du produit augmente.
Exemples
- La jidoka est principalement utilisée dans les industries manufacturières et automobiles ; cependant, elle peut également être démontrée dans des produits simples utilisés dans la vie quotidienne.
- Par exemple, si votre armoire de cuisine est fixée avec une poubelle, vous remarquerez que lorsque vous ouvrez la porte de l’armoire, le couvercle de la poubelle est automatiquement soulevé.
- C’est parce qu’il y a une ficelle qui aide à soulever le couvercle de la poubelle au moment où la porte est ouverte.
- Pensez à une machine à imprimer. S’il manque une feuille dans la machine, un détecteur de feuilles soulève le cylindre d’impression. Ceci est dû au Jidoka.
- Dans l’industrie manufacturière, un détecteur est utilisé pour vérifier si les composants sont alignés. Même si une petite pièce n’est pas alignée, la machine est arrêtée.
- Certaines machines de haute qualité utilisent la procédure de rappel. Parfois, malgré les meilleures contre-mesures, certains produits de la chaîne de production peuvent glisser dans le cycle de la machine, sans être détectés. La procédure de rappel vérifie chaque produit une fois de plus, avant l’éjection finale de la sortie.
- Les rideaux lumineux sont utilisés dans les machines d’alimentation automatique. Ils disposent d’un capteur de présence qui arrête la machine si un composant est cassé ou est défectueux.
Avantages du Jidoka
- Il permet de détecter le problème le plus tôt possible.
- Il augmente la qualité du produit par une mise en valeur et une normalisation appropriées.
- Il intègre la puissance de la machine à l’intelligence humaine pour produire des marchandises sans erreur.
- Il aide à une utilisation appropriée de la main-d’œuvre puisque le processus est automatisé, les travailleurs peuvent passer leur temps à effectuer des services à plus grande valeur ajoutée.
- Il y a moins de possibilités d’erreurs dans la production, ce qui augmente considérablement le taux de productivité et réduit les coûts.
- L’amélioration de la satisfaction des clients est également un avantage important.
- Des produits de qualité sont fabriqués en moins de temps.
Jidoka est l’un des piliers forts du TPS (Toyota Production System). Il permet de prévenir les défauts dans le processus de fabrication, d’identifier les zones de défaut et de concevoir des solutions pour que le problème soit corrigé et que le même défaut ne se reproduise pas. Le Jidoka aide à construire la « qualité » et a considérablement amélioré le processus de fabrication.